One of Toptech Systems’ customers needed to streamline operations at their marine loading operations. The goals were to increase efficiencies and accommodate new blending requirements.
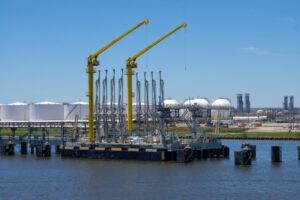
The customer has a highly complex Distributed Control System (DCS) delivering a variety of products, each loaded through different meters and loading arms that required manual intervention. Additionally, there was no automatic document printing, and operators had to manually enter all meter readings into the ERP system.
This problem is not unique. Often, metering lines are engineered to deliver specific blend ratios. However, today, there is a greater need to quickly adapt to alternative fuel products. These fixed metering lines simply do not offer the flexibility to accommodate these new products, the wide blend ranges , or even allow those ratios are being created due to meter restrictions..
For example, blending diesel from high and low sulfur components requires varying blend ratios based on the end specifications and the conditions of the base components. In a setup with two base components, each with its own meter, the blend ratio is limited by the flow meter specifications. This can reduce load efficiency and accuracy. Blending biocomponents like ethanol and FAME into regular hydrocarbon products is becoming standard. For a 95/5% blend, the biocomponent must flow much slower than in a 5/95% blend, affecting accuracy as the meter operates at its minimum flow rate.
To improve efficiency, it would be ideal if you could run any product through any meter, while safeguarding meter accuracy and desired blend ratios. That is where the Multiload II+ Routing feature comes in.
Instead of each component fixed to a specific meter, Routing provides a flexible setup, allowing you to assign blend components to the most suitable meter for the job. It assigns multiple components to multiple meters, rather than a more traditional (and inefficient) one-to-one relation between a product component and a meter.
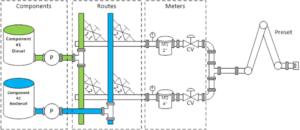
When authorizing a blend, Multiload II+ uses a configurable algorithm to automatically select the best product routes. Routes are assigned depending on external inputs, custom logic, blend percentages and target flow rates. The MultiLoad II+ unit even allows to assign a cost to a certain routing option. MultiLoad II+ intelligent algorithm will then decide, based on all parameters, to line up the most cost effective routing option to perform the blending operations.
Routes can be set up for new alternate fuel blending skids, as well as existing configurations, reducing costs compared to re-engineering your DCS.
As a result of implementing the Multiload II+ Routing layer, the customer was able to simplify their DCS and reduce manual intervention. By using MultiLoad II+ and modernizing the DCS/SCADA, the customer can load more efficiently, and without errors. Additionally, every transaction rolls ups to Toptech Systems’ Terminal Automation System (TAS) TMS7, which integrates with the customer’s ERP system for easy and reliable billable purposes.
To learn more about the Routing feature in Multiload II+ and the top 3 reasons to choose Multiload II+, contact us to request a Return on Investment (ROI) report.